Semi-Automated Pallet Runners & Pallet Shuttles
Pallet runners are semi-automated deep lane storage systems that delivers pallets via a cart that runs on a track within the racking system. It's also commonly referred to as a pallet shuttle system.
Pallet runners eliminate the need for wider picking aisles, since the lift trucks do not need to enter into aisles to retrieve product. It essentially allows the entire volume of your warehouse to be utilized. The carts can be outfitted to suit a wide variety of pallet designs and can be used for first-in, first-out (FIFO) or last-in, first-out (LIFO).
REB Storage Systems International is a material handling systems integrator that provides full project management of pallet runner and pallet shuttle systems. Our services include design, permitting support, subcontractor management, procurement of materials, and installation.
Read below to learn more about REB’s semi-automated pallet runner and pallet shuttle systems.
How a Pallet Runner System Works
In a system utilizing semi-automated pallet runners, pallets are loaded into the system by a lift truck then transported and placed on the rack by an automated cart.
The process of unloading is the same: the cart collects and transports pallets out of the system, while an operator moves between the lane and the shipping dock or other destinations. Once the cart collects the pallet, it transports it to the home position. There are a number of retrieval options, including:
- Continues out – cart retrieves all pallets in a row until empty.
- Controlled retrieval - operator can select number of pallets it would like to retrieve, which eliminates miscounting.
- Inventory count – cart will count number of pallets in row.
Submit Your Inquiry
REB’s Turnkey Services for Pallet Runner Systems
REB provides full project management of your pallet runner system. A REB project manager will be your point of contact throughout the project. Our project managers prioritize communication and will make sure that all applicable parties have a firm understanding of timelines and progression of the project.
Read below to better understand our pallet runner system project management services.
Design Services
The first step in REB's design services is to speak with your REB account executive so that we thoroughly understand the scope of your project. If necessary, we’ll conduct an onsite assessment. We want to make sure we understand your goals and current pain points so that we provide you with a solution that is optimized to your operation.
During the design process, we’ll obtain information such as your SKU profiles, space restrictions, and picking processes. We’ll work with you to ensure that your pallet runner system is set up to suit your requirements. For example, if you require your system to have a first-in, first-out or a last-in, first-out product flow.
Once all information is obtained, REB project designers will create a CADD drawing of your pallet runner system that suits all space and picking process requirements.
Permitting Support
If necessary, we’ll evaluate if permitting for your pallet runner system is required through our permitting support services. If permits are required, we’ll put together and submit all drawings and other documentation needed for permit approval. This often includes a high pile storage report.
Subcontractor Management
Once your pallet runner system design is finalized, your REB project manager will secure all suppliers and subcontractors. We’ll manage their involvement through the project. This includes freight and installation.
Our project management services prioritize communication and will make sure that all applicable parties have a firm understanding of timelines and progression of the project.
System Installation
REB Storage Systems has more than 60 years of professional experience installing material handling systems in warehouses nationwide. We’ll ensure that your operation’s pallet runner system is safely installed and compliant with MHI & OSHA standards while it optimizes your storage space and improves efficiency.
Is A Pallet Runner System Right For Your Operation?
A pallet runner system is ideal for a number of applications, including:
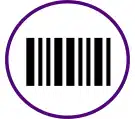
High number of pallets of the same SKU: with this system, each lane should have the same SKU. The greater number of pallets that have the same SKU, the more lanes you’ll be able to fill in the pallet runner system.

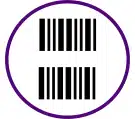
Low number of SKUs: in this type of system, lanes are usually dedicated to a single SKU. So the lower the number of SKUs, the less lanes you’ll need (depending on the volume of your SKUs). It is possible to have a high number of SKUs with this system, but the more SKU’s, the more lanes that will be needed.
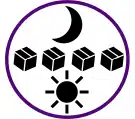
Requires staging pallets for shipments: this system can be used for a better staging operation. For example, the night shift can stage each lane with all pallets that need to be loaded onto each truck the next day. That way, the day shift can quickly unload the already built load from a lane to be loaded onto the corresponding truck.
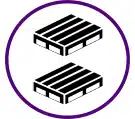

Requires specialized pallet configuration: pallets do not touch one another in this system. This allows for products to be transported ‘gently’ throughout the system. Some examples of specialized pallet configurations that can benefit from this include:
- Product that is non stackable or that can only be stacked 2-high.
- Product required to be displayed a certain way on pallets
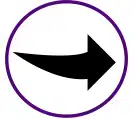
Fast throughput: this system is best for products that don’t ‘sit around’. Since lift truck drivers don’t have to drive into the system, the driver can retrieve a pallet, and while they drive it to the loading dock the next pallet can be retrieved from the system and be ready for the driver when they make it back to the system. This lends to fast throughput. Also, multiple drivers can be retrieving from the system at once.

Maintain good quality pallets: the pallet runner carts go under the pallets in this system. Because of this, there can’t be any sagging or obtrusions from the pallet. Grade A or refurbished Grade B are required for the system to operate properly. It’s also typically advised to not use cardboard pallets or pressboard pallets in a pallet runner system, as these commonly cause problems.
Advantages of a Pallet Runner
Once you’ve assessed the prior information and have concluded that a pallet runner is a good fit for your operation, but are still unsure, you should consider some of the advantages pallet runner has over other pallet racking systems.
It should be noted that while a pallet runner can have certain advantages over other racking types, this is only if it’s a fit for your operation. There are situations in which a rack system will be advantageous over a pallet runner system. A material handling integrator, such as REB, can help you assess your operation and help you determine if this is indeed a good fit for you.
Pallet Runner Advantages Over Drive-In Rack
Reduced rack damage and product damage: with drive-in there are many potential points of impact, since the forklift operator spends a large portion of loading and unloading the system within the rack structure itself. You can add guide rails to prevent left or right movement of a forklift, however you still have the potential for vertical damage from the mast and also there is a high potential for product damage.
Furthermore, when a drive-in system has impact, especially from within the middle of the structure, it can cause further damage from around that impacted area or complete failure of that area.
With a pallet runner system, the operator interacts only with the charge and dis-charge end. So even if damage occurs, the impact is minimal, only affecting the impacted side.
Also, on drive-in racking the only support linking rack in the lateral direction is a top cross tie and the back frames. With pallet runner, the entire system is tied together at every level and every frame, making it a much sturdier structure.
Deeper lanes, providing higher storage density: a drive-in rack system can technically go as deep as needed, however there are factors that limit how deep you can go. One example is the deeper you go, the higher the possibility of more damage via forklift in deeper lanes. So again, going back to the damage, that becomes more of an issue the deeper you go. This is then highly difficult to either repair or replace.
Also, the deeper you go in drive-in rack, the more difficult it becomes to retrieve the pallets. So operational efficiency can become compromised.
Pallet runner is basically unlimited as to how many pallets deep it can be. The longest pallet runner system in the world is 83 pallets deep. And the issues mentioned in regards to deep lane storage in drive-in rack are basically nonissues in a pallet runner system.
Each level is independently accessible, resulting in less honeycombing: Honeycombing is when you have blank pallet positions within your rack system. In a drive-in system, pallets below and above the required pallet can get in the way, and drivers often have to move these obstructions first. This is not the case in a pallet runner system.
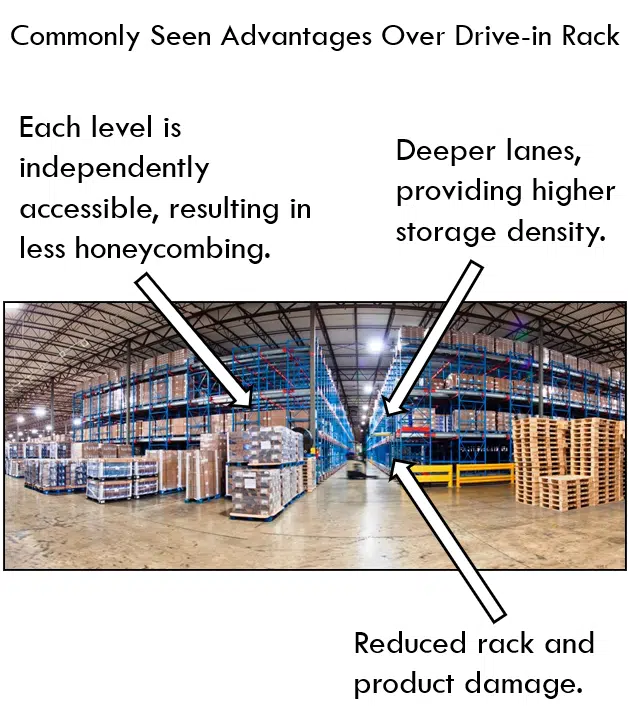
Pallet Runner Advantages Over Push Back Rack
Does not require particular lift trucks: Lift trucks for a push back system require an appropriate amount of power based on pushback force as a result of the weight of multiple pallets having to be pushed. In a pallet runner system, the lift truck power only needs to accommodate one pallet.
Can be designed for both FIFO (first-in, first-out) and LIFO (last-in, first-out): push back is LIFO only.
There are a few ways that a pallet runner system can be used as a FIFO:
- Pallets can be loaded in one end and unloaded from the other.
- The system can be designed to have ‘bi-directional’ capability. This allows the home position to switch from one end to the other. This is more common in larger systems.
- The system can be designed to have ‘split lanes’. For example, in a 30 pallet deep system, the first 26 pallet positions can be designated as LIFO, while the last 4 are designated as FIFO.
Deeper lanes: push back traditionally can only be designed up to 6 pallets deep, Pallet runner systems have been designed and successfully implemented for up to 83 pallets deep.
Does not require product-to-product contact to work correctly: this lessens the likelihood of product damage.
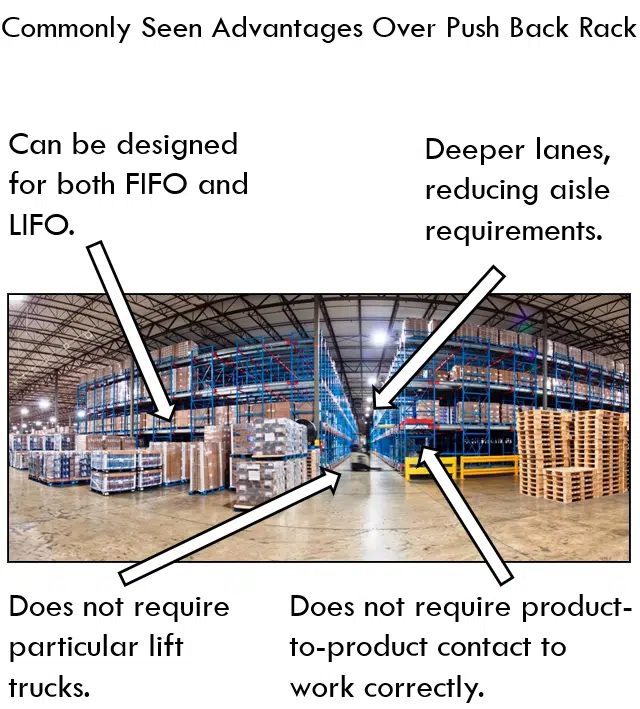
Pallet Runner Advantages Over Pallet Flow Rack
Level system, no need for pitch: a pallet flow system requires a pitch so that gravity can move pallets from the back loading side to the front retrieval side. This pitch can result in vertical loss of space. The deeper a pallet flow system, the greater the loss of vertical space. Additionally, lightweight product will need higher pitch which is loss of vertical space.
Controlled product flow, no relying on gravity: this lends to a number of advantages including lessoning the likelihood of product damage.
Pallet runner is not affected by varying pallet weights: for a pallet flow system to work properly, pallet weights should be consistent. While a pallet runner system does require high-grade pallets as does a pallet flow system, it does not require a certain pallet weight.
Click here to view a case study that compares a pallet flow rack system with a pallet runner system.
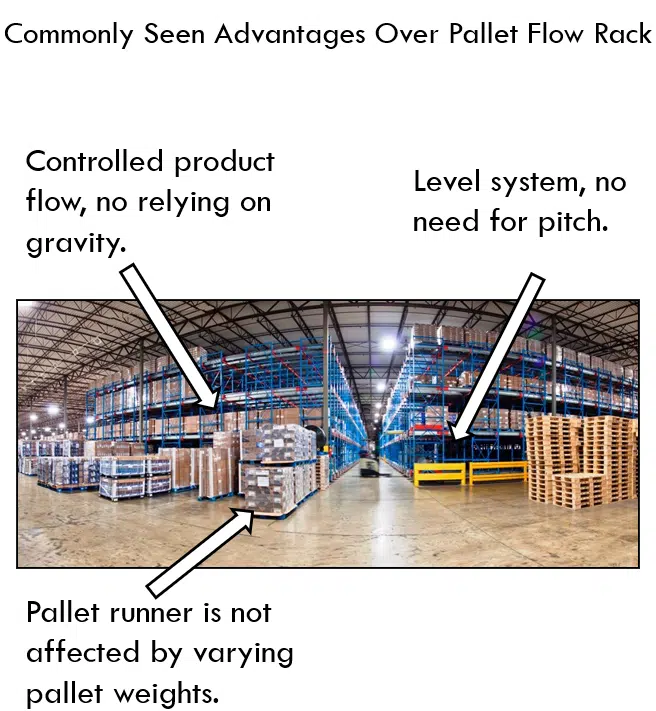
Your Next Step For A Pallet Runner System
Whether your next step is to gather more information or request a quote, consider REB Storage Systems International.
REB is highly knowledgeable and experienced in designing, project managing, and installing automation and racking solutions. We will make sure your system is the best fit for your SKU profiles and space. We work with you to provide a turnkey system. From design, product procurement, subcontractor management, install, and permitting support, REB handles it all for you.
REB is a highly experienced systems integrator, in business since 1962. REB has 17 in-house project managers and project designers, all highly experienced in the material handling industry. These people know this industry inside and out.
We’d appreciate the opportunity to help you further, whether that be more information or a quote. Fill in the contact form on this page or call us at (800) 252-5955 to get in touch with a REB representative.