Vertical Lift Modules (VLMs)
Vertical lift modules, commonly referred to as a VLM, is a semi-automated material handling solution. A VLM is an enclosed system of vertically arranged trays stored in both the front and rear with an extractor device operating in the center. With the push of a button or scan of a barcode, the required items are retrieved by the VLM and brought to the picker. This process eliminates the need for pickers to travel and locate each required item, decreasing overall pick times. VLMs are especially beneficial for kitting and batch picking.
In vertical lift modules, trays are stored using the least amount of space, ensuring maximum storage density within the VLM. This is accomplished by the system scanning the height of the products going back into the system and placing that tray in the ideal storage location slot. In one case study, the VLM saved a company 75% of floor space compared to the racking they were using.
REB Storage Systems International is a material handling systems integrator that provides full project management of vertical lift module systems. Our services include design, permitting support, subcontractor management, procurement of materials, and installation.
Read below to learn more about REB’s vertical lift module systems including how they work, ideal uses, commonly seen advantages, and details on REB's services.
How Vertical Lift Modules Work
Vertical lift modules automatically deliver trays with the stored items to an access window with a push of a button or a scan of a barcode. They can also generate a list directly imported from an ERP.
VLMs are modular, meaning that you can easily add or remove trays as well as add or take away height if you move it to a different location with different height restrictions.
Vertical lift modules can be setup as stand alone systems, or can be connected to a WMS. This system will also generate a number of reports for as needed. These reports can include quantity on hand, which items have been accessed and who accessed them, and so on. There are a number of standard fields and up to 8 customizable fields that you can have the system track and report on.
Submit Your Inquiry
Here’s an example of the steps taken in a vertical lift module:
- Picker scans a barcode or pushes a button associated with the item needed.
- VLM retrieves the product and presents the tray via the access window.
- A laser pointer or LED screen will identify the specific pick location on the tray.
- Once the item is picked, the picker indicates to the VLM that the task is complete.
- The VLM repeats this action for the next item on the scanned list.
REB’s Turnkey Services for Vertical Lift Module Systems
REB provides full project management of your vertical module system. A REB project manager will be your point of contact throughout the project. Our project managers prioritize communication and will make sure that all applicable parties have a firm understanding of timelines and progression of the project.
Design Services
The first step in REB's design services is to speak with your REB account executive so that we thoroughly understand the scope of your project. If necessary, we’ll conduct an onsite assessment. We want to make sure we understand your goals and current pain points so that we provide you with a solution that is optimized to your operation.
During the design process, we’ll obtain information such as your SKU profiles, space restrictions, and picking processes. We’ll work with you to ensure that your vertical lift module system is set up to suit your requirements. For example, if you require your system to have a first-in, first-out or a last-in, first-out product flow.
Once all information is obtained, REB project designers will create a CADD drawing of your vertical lift module system that suits all space and picking process requirements.
Permitting Support
If necessary, we’ll evaluate if permitting for your vertical lift module system is required through our permitting support services. If permits are required, we’ll put together and submit all drawings and other documentation needed for permit approval. This often includes a high pile storage report.
Subcontractor Management
Once your vertical lift module system design is finalized, your REB project manager will secure all suppliers and subcontractors. We’ll manage their involvement through the project. This includes freight and installation.
Our project management services prioritize communication and will make sure that all applicable parties have a firm understanding of timelines and progression of the project.
System Installation
REB Storage Systems has more than 60 years of professional experience installing material handling systems in warehouses nationwide. We’ll ensure that your operation’s vertical lift module system is safely installed and compliant with MHI & OSHA standards while it optimizes your storage space and improves efficiency.
Is a Vertical Lift Module System Right for Your Opertation?
Vertical lift modules are ideal for a number of applications, including:
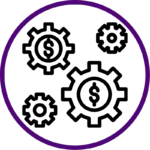
High value items: a secured locking door keeps items locked away. You can also include a feature where it requires a second authorization or manager-level clearance. You can restrict this by individual tray.
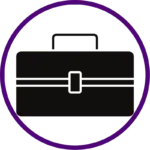
Kitting: For example, when building a GPS unit you can have all required parts, such as the screens, buttons, and circuit boards, on the same tray.
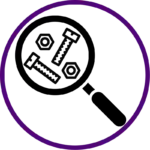
Small parts / partial case picks: Individual, organized treys make it easier to keep track of and store small parts. Small parts are typically harder to manage and result in more mispicks.
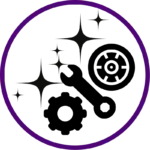
Parts that need to remain clean: Since the inventory is stored in an enclosed unit, it keeps items clean. Especially for slow-turn inventory.
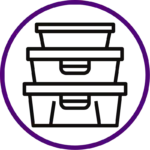
Batch picking: VLMs can pull exact quantities needed in order to fill multiple orders at once. The machine will clearly indicate to the operator the exact quantity of the SKUs needed in order to fulfill each order. This minimizes the time spent by the operator at each SKU location.
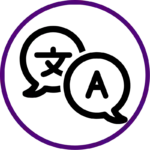
Multilingual warehouses: VLMs are fluent in 28 languages. Each pickers profile can be setup with their preferred language, which the machine will recognize when they login.
Advantages of Vertical Lift Modules
Once you’ve assessed the prior information and have concluded that a vertical lift module is a good fit for your operation, but are still unsure, you should consider some of the advantages that vertical lift modules provide. Commonly seen advantages include:
Reduced labor costs: by delivering items directly to the operator, travel and search time commonly associated with a rack system is drastically reduced. This allows the operator to spend more time picking, increasing overall productivity. It's been shown to provide up to 2/3 less labor costs.
Increased picking speed: VLMs can increase productivity up to 500%. This is due to the machine locating and presenting each item, which is done in 30 seconds or less. This feature eliminates 'dwell time' the picker may spend searching an aisle.
Another feature that helps increase pick speed is that the VLM learns overtime. It will learn which products are your fast movers, and will adjust the location of where they place those trays within the system so they are more readily available.
Eliminates dwell time: Less time spent in the aisle pulling the product. The machine presents the item to you upon request in less than 30 seconds, on average.
Saves 75-88% of the footprint: meaning that by consolidating a racking or shelving system into a VLM, you will free up 75% - 88% of the current floorspace being used to store.
Additionally, VLMs can support up to three access openings (vertically), so it can be used in a multi-floor operation. This can be accomplished either via multiple floors or via mezzanines.
Eliminates shrinkage: the machine tracks everything. It knows who used it last, what they did, and so much more. There are reports that can be generated to see this information.
Improved ergonomics: the machine will compensate for the height of the picker. The picker's preferred picking height is specified in their profile setup in the system and recognized upon employee sign in.
Integrating Vertical Lift Modules
Incorporating VLMs into an integrated material handling system is very beneficial. By including a VLM as a part of a full system it will improve the efficiency of a distribution center.
There are a variety of solutions that are good complements to a vertical lift module. Some of which include:
- Conveyors: can help transport items from the VLM system to the packing and shipping areas.
- Put-to-light wall: product can be picked from the VLM and then transferred to the put wall. This helps make sure that the items are placed in the proper cartons for shipping more efficiently.
- Pallet racking: pallet racking helps store any overflow product that the VLM does not have room for at the moment.
Your Next Step for a Vertical Lift Module System
Whether your next step is to gather more information or request a quote, consider REB Storage Systems. REB is a highly experienced systems integrator, in business since 1962. REB has 17 in-house project managers and project designers, all highly experienced in the material handling industry. These people know this industry inside and out.
REB is highly knowledgeable and experienced in designing and installing vertical lift modules and will make sure your system is the best fit for your space. We work with you to provide a turnkey system. From design, products procurement, subcontractor management, install, and permitting support, REB handles it all for you.
We’d appreciate the opportunity to help you further, whether that be more information or a quote. Fill in the contact form on this page or call us at (800) 252-5955 to get in touch with a REB representative.