Warehouse Pick Modules
Pick modules integrate a variety of material handling solutions to optimize the flow of orders. They move product efficiently through a distribution center and expedite the order fulfillment process.
The design of warehouse pick modules can be for manual pick applications, automated pick applications, or a combination of both. These integrated systems consolidate space and create an efficient distribution center, reducing or eliminating walking time, and saving on labor costs.
Typical Components and Layout of a Pick Module
Warehouse pick modules can include a number of elements in one design to produce the optimal layout and flow process for your operation:
Submit Your Inquiry
Pick module layouts vary, but often contain areas to accommodate faster moving and slower moving products, and/or palletized products and piece picking. These areas are sometimes referred to as forward pick and reserve storage areas.
Warehouse pick module systems can be designed as one level, or utilize mezzanines to create a multi-level pick module. Systems can also be designed so that it's initially one level, but can be expanded vertically in the future. Read this case study for an example of this.
Benefits of Using Pick Modules
Pick modules can provide numerous benefits in a distribution center. These include:
- Shortened order fulfillment cycle times
- Increased pick accuracy
- Increased selectivity
- Increased density
- Labor reduction
Optimize Your Pick Module with REB's Proven Process
In order to achieve desired outcomes from your warehouse pick module, the right design of material handling solutions must be integrated. This is why it's so important to use an experienced material handling integrator, such as REB Storage Systems, to help design and build your system.
There are a number of steps REB will work through with you in order to achieve your optimal solution:
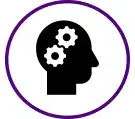
Your account executive will gain a thorough understanding of your operation. This includes number and types of SKUs, available space, throughput requirements, and current material handling methods used.
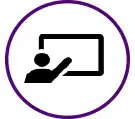
Your account executive will then educate you on material handling system options that make sense for your operation.
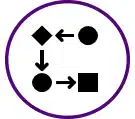
Based on your feedback, REB designers will develop a layout that optimizes your space and SKUs.
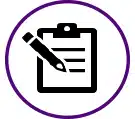
Once the layout is approved, REB will then source materials and subcontractors based on pricing and lead time. You'll then be presented with a proposal.
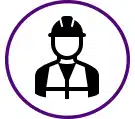
Upon acceptance of the proposal, you'll be assigned a REB project manager. The project manager will manage the entire pick module implementation through completion. This includes product procurement, subcontractor management, freight management, and permitting support.
Your Next Step for a Pick Module
Whether your next step is to gather more information or request a quote, consider REB Storage Systems. REB is a highly experienced systems integrator, in business since 1962. REB has 17 in-house project managers and project designers, all highly experienced in the material handling industry. These people know this industry inside and out.
REB is highly knowledgeable in all areas of racking and automation options and will make sure your pick module system is the best fit for your SKU profiles, space, and growth projections. We work with you to provide a turnkey system. From design, products procurement, subcontractor management, install, and permitting support, REB handles it all for you.
We’d appreciate the opportunity to help you further, whether that be more information or a quote. Fill in the contact form on this page or call us at (800) 252-5955 to get in touch with a REB representative.