Rack Safety Inspections
Regularly having a rack safety inspection to identify and repair safety concerns is important. It can help avoid a rack collapse, damage to property, and on the extreme end, employee injury.
REB Storage Systems International has a dedicated rack safety and repair team. Our knowledge of rack safety best practices and ANSI/RMI rack safety standards allow us to analyze a rack system, locate all possible risks, and make suggestions to help you increase employee safety and asset protection.
Read below to learn more about REB’s rack safety inspections and why they should be an important part of your operation.
What Can Cause an Unsafe Rack System?
There are several factors that can contribute to a rack system not complying with safety regulations. Daily use of the system can result in both obvious damage as well as not so obvious damage.
Submit Your Inquiry
Keep in mind that rack systems are complex, engineered structures. Even a slight bump can compromise the integrity of the system.
Here are some things that commonly contribute to an unsafe rack system:
- Forklifts bumping into the rack system.
- Reconfiguring beam levels in-house to better accommodate products.
- Safety clips being unknowing knocked off.
- Anchors not being properly installed or sheared off.
Our Rack Safety Inspections Ensure You Comply with Rack Safety Regulations
The American National Standards Institute (ANSI) along with the Rack Manufacturer’s Institute (RMI) have established a set of regulations regarding rack safety and repair.


These regulations, which are laid out in detail in ANSI/RMI 16.1, state that owners of industrial pallet rack systems, movable shelf racks, and stacker racks made of cold-formed or hot-rolled steel structural members should adhere to the following:
Repair and Replacement of Damaged Components: These shall be replaced by qualified persons following recommended and documented procedures. Repair components must be at least as strong as undamaged components.
The repair process (assessment, design, and installation) should be overseen by a qualified rack design engineer (supervising engineer). The assessment and design of rack repairs should address all loads that can be imparted on damaged members (static, seismic, etc.), not just on the specific members being repaired.
Owner Maintenance: The owner shall maintain the structural integrity of the installed rack system assuring proper operational and maintenance procedures. Regularly inspect for damage and immediately unload the affected area and replace or repair the damaged column(s), beam(s), and other structural components.
Owners should avoid attempts to repair rack despite possibly having personnel or resources in their facility to attempt repairs. Without proper engineering oversight, there is no proof or assurance that the repair is sound and will yield a safe operating system.
Additions, Alterations, and Reconfigurations: All additions, alterations and reconfigurations should be reviewed by a qualified engineer to ensure any changes meet the same requirements as the original installation. Engage a licensed professional engineer to review the proposed racking configurations.
Rack Damage: Upon any visible damage, the pertinent portions of the rack should be unloaded immediately by the user until the damaged portion is repaired or replaced. Contact a qualified representative for an evaluation of the effects of the damage to the structural integrity of the rack system. Only after such an evaluation (after repairs if necessary are competently completed, and after approval of the work is done) should the rack section be returned to service.
To learn more about rack safety regulations set forth by ANSI/RMI as well as OSHA, visit our article, Pallet Rack Safety Guidelines: What They are and How to Comply.
What to Expect During REB’s Rack Safety Inspection
The purpose of REB’s professional rack safety inspection is to ensure the rack system meets ANSI/RMI rack safety standards.
First, one of our rack safety experts will conduct a full walkthrough of your facility. They will inspect the full scope of the rack to identify all damage and safety concerns.
Next, you'll be provided with a scope drawing that identifies the location of all damage and what type of damage it is.
"REB's superior rack remediation project management process is evidence they've built the model for the rack repair services business that works."
- Doug Berry
Iron Mountain
After reviewing your damage summary, you can then decide if you'd like to move forward with any or all the repairs. Upon your request, you’ll receive a proposal and a corresponding scope drawing for these services.
Safety Concerns That Are Inspected
REB’s professional safety inspections focus on two main areas: damage concerns and protection recommendations. Specifically, the degree and type of damage is identified to determine whether repair or replacement is needed.
Rack Damage Concerns
Damage concerns that can be identified during a rack safety inspection include:
Column Damage: Any rips, tears or deflection beyond acceptable limits. Deflection greater than ½” can no longer carry the original rated load.

Horizontal and Diagonal Strut Damage: Broken welds, missing braces, or braces with rips, tears or deflection beyond acceptable limits.

Footplate Damage: Sheared or twisted beyond acceptable limits.
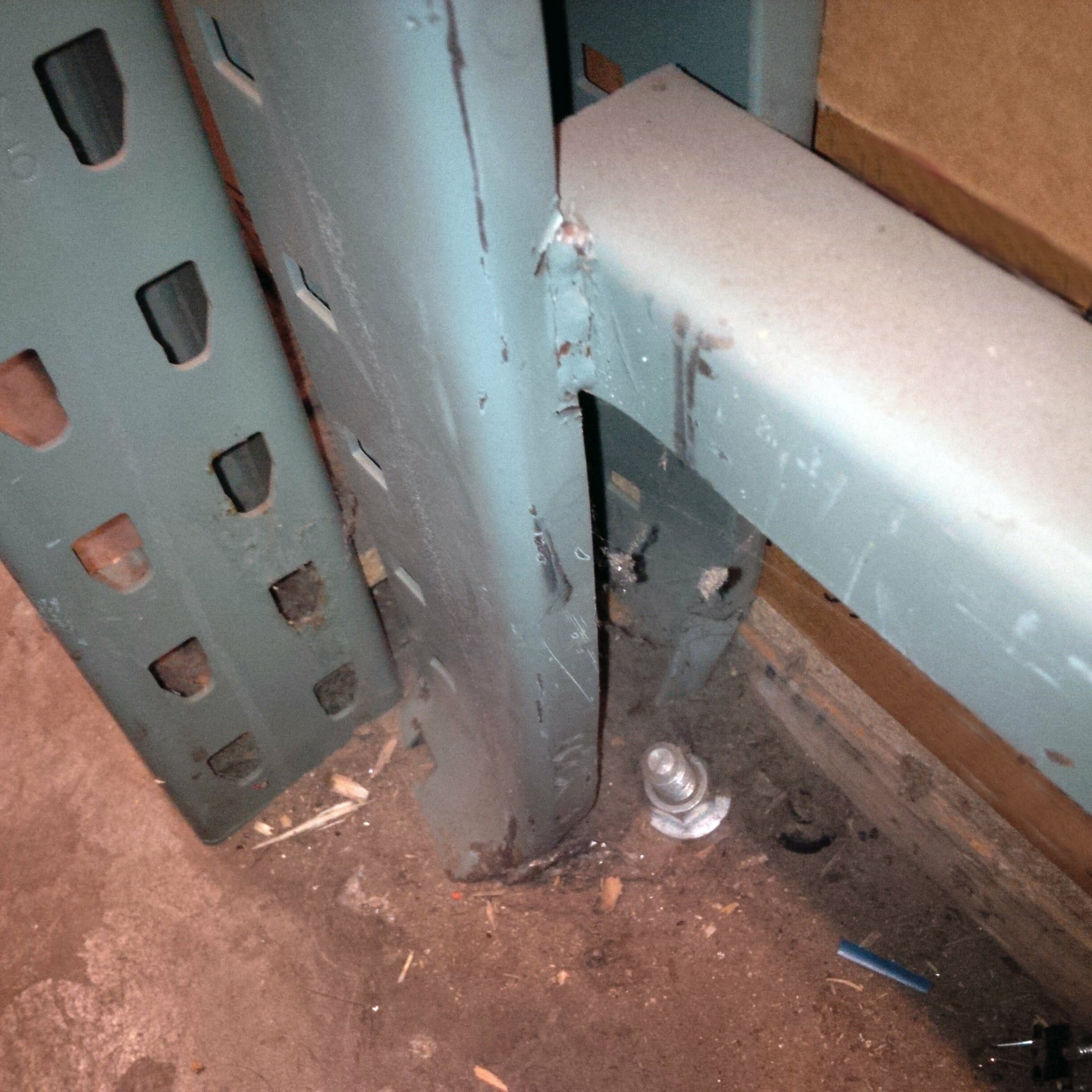
Overloaded Beams and Frames: Any beam that exceeds the rack manufacturer’s capacity (capacity is based on evenly distributed loads).
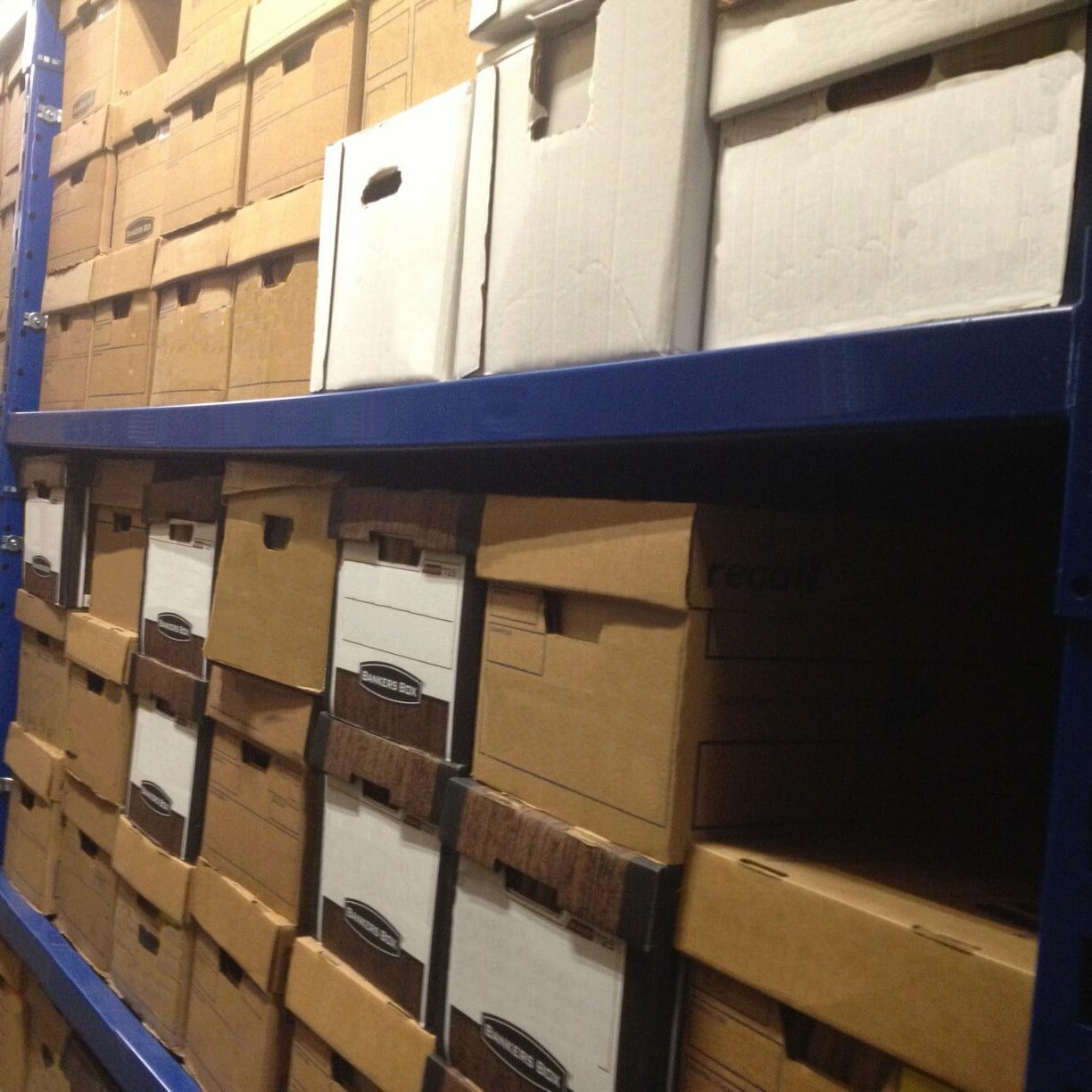
Anchor Damage: Missing, broken or loose anchors are problematic because each upright footplate, both the front and back, must be anchored to the floor.
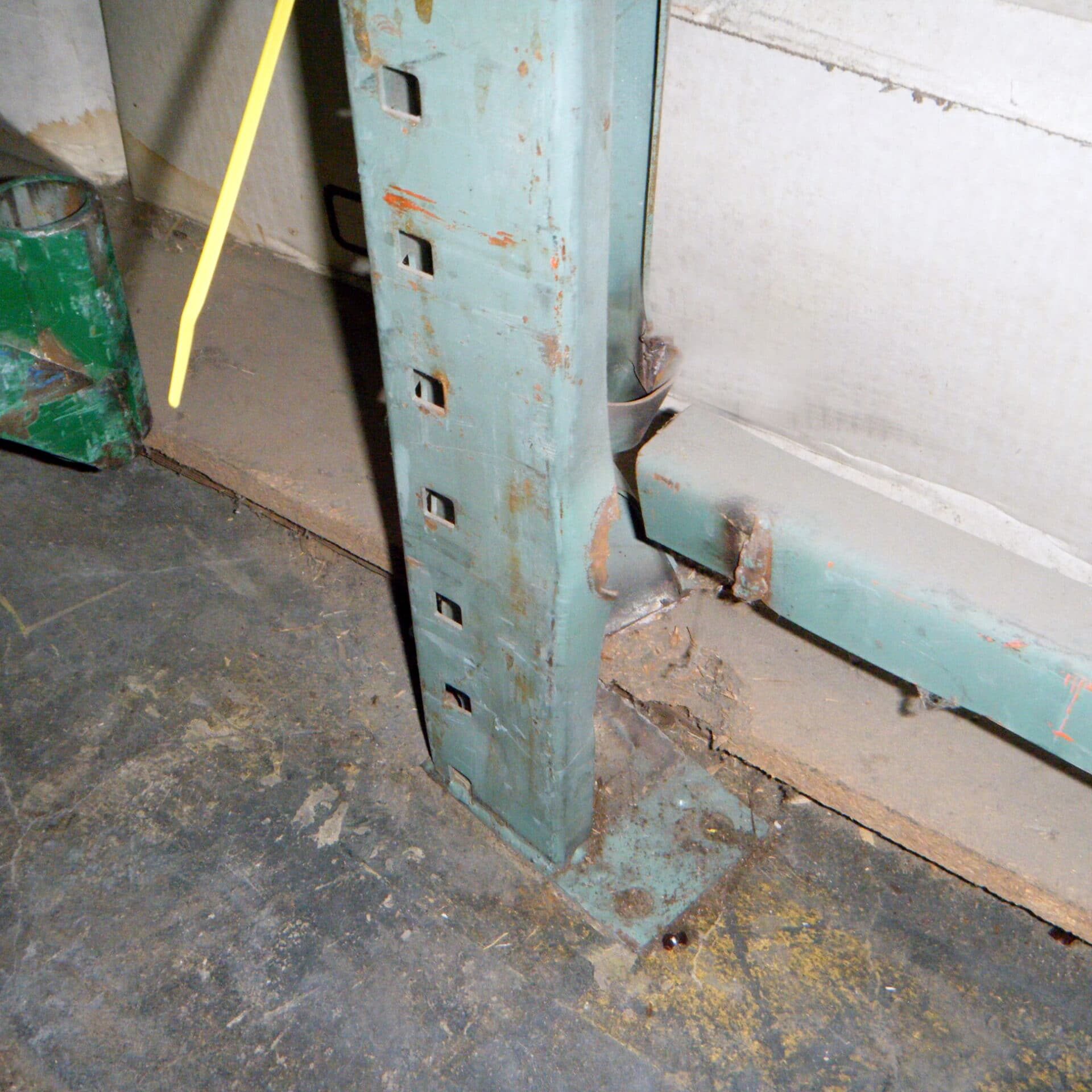
Missing or Damaged Components: Wall ties, cross-aisle ties, crossbars, beam safety pins, wire mesh decks or pallet stops.
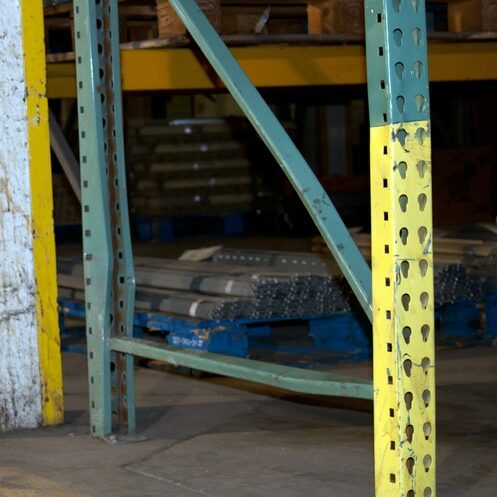
Beam Damage: Missing or damaged beams; loose, damaged or missing fasteners; or deficiencies in load locks and snap locks.

Leaning Frames: A minimum plumbness and straightness (both cross and down aisle) of 1/2"per 10' of height.
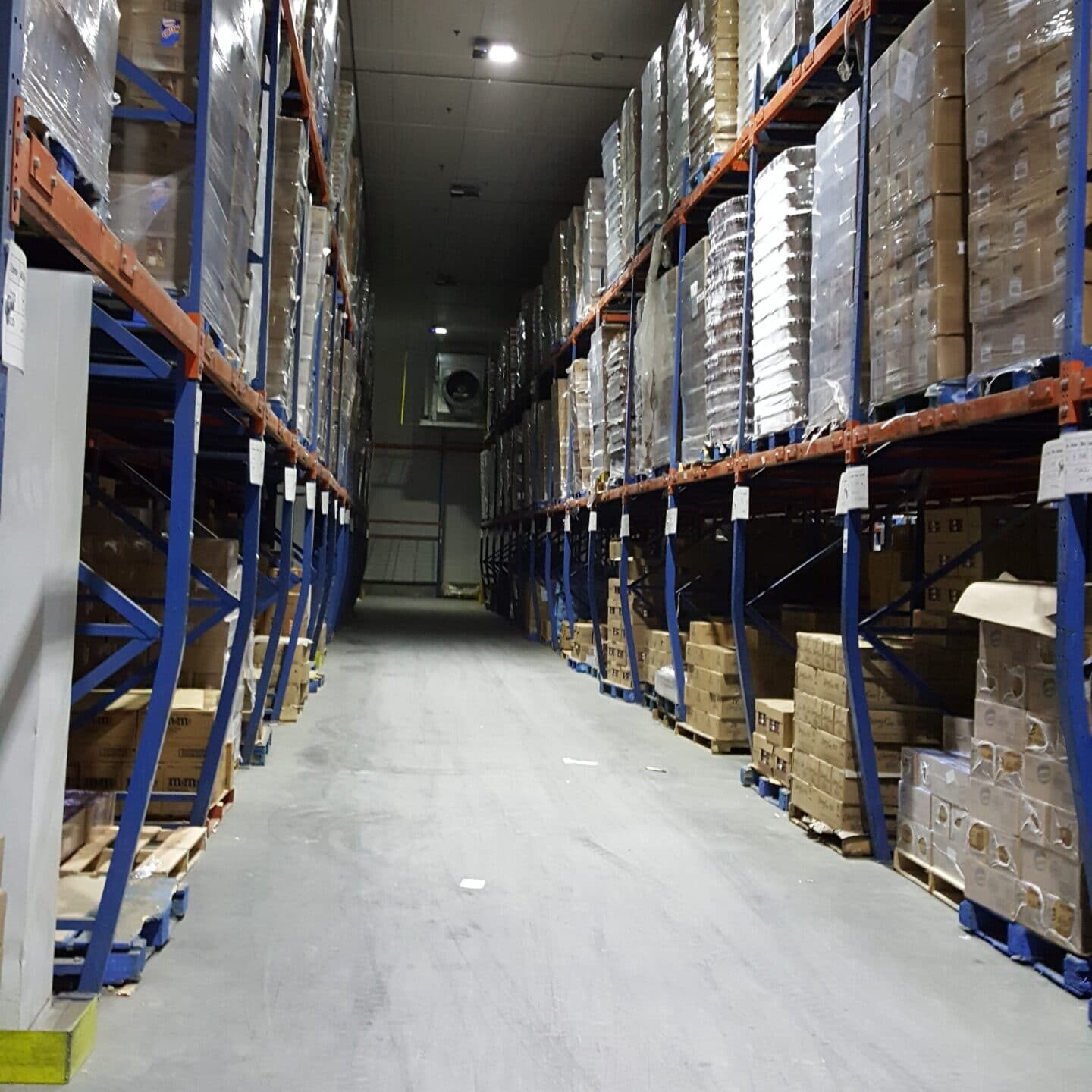
Damaged Decking: Exposed jagged edges, dips or missing pieces.
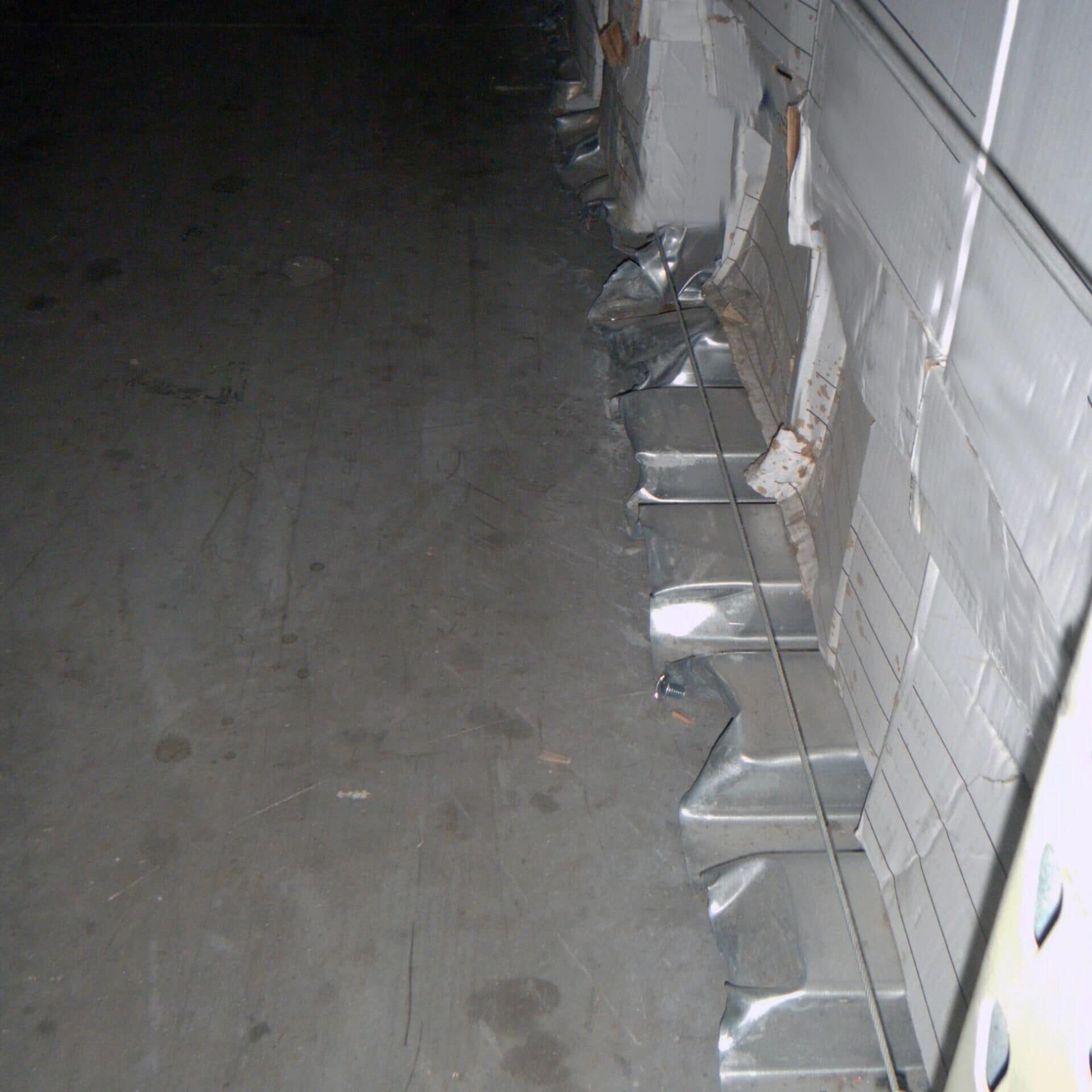
Rack Protection Recommendations
We will also offer recommendations for rack protection items that can help avoid future rack damage, inventory damage, and/or employee injury. These include:
- Post protectors
- Frame extensions
- Down aisle protection
- End of row protection
Visit our rack protection page to learn more about these.
Repair and Replacement Services
Once we complete the rack inspection, we’ll follow up with a scope drawing that details all repair and/or replacement recommendations.
The most common issue found is upright damage. This is because it’s typically the most obvious sign of an unsafe rack system, and often the reason a company requests a safety inspection.
In many cases, rack repair, as opposed to rack replacement, is a time and cost-effective option. Visit our rack repair page to find out more about the rack repair process.
Recommended Frequency of Rack Safety Inspections
There are two methods to consider when deciding on the frequency of your rack safety inspections: professional safety inspections and in-house safety inspections.
As detailed in our article, When To Conduct Warehouse Pallet Racking Safety Assessments, in-house assessments should be done in-between professional inspections. A professional rack safety inspection should be conducted based on your operational throughput, system layout, and general use and wear-and-tear of the system. But in general, it’s not recommended to go more than one year without having a professional inspect the safety of your rack system.
Take the Next Step for a Safe Rack System
If you’re concerned about the safety of your racking system, consider REB Storage Systems.
We have a dedicated team of rack safety professionals who conduct rack safety inspections for our nationwide customer base. We are highly experienced in identifying rack safety concerns and stay up to date on all rack safety regulations.
We’d appreciate the opportunity to help you further, whether that be more information or a quote. Fill in the contact form on this page or call us at (800) 252-5955 to get in touch with a REB representative.
Case Studies To Consider
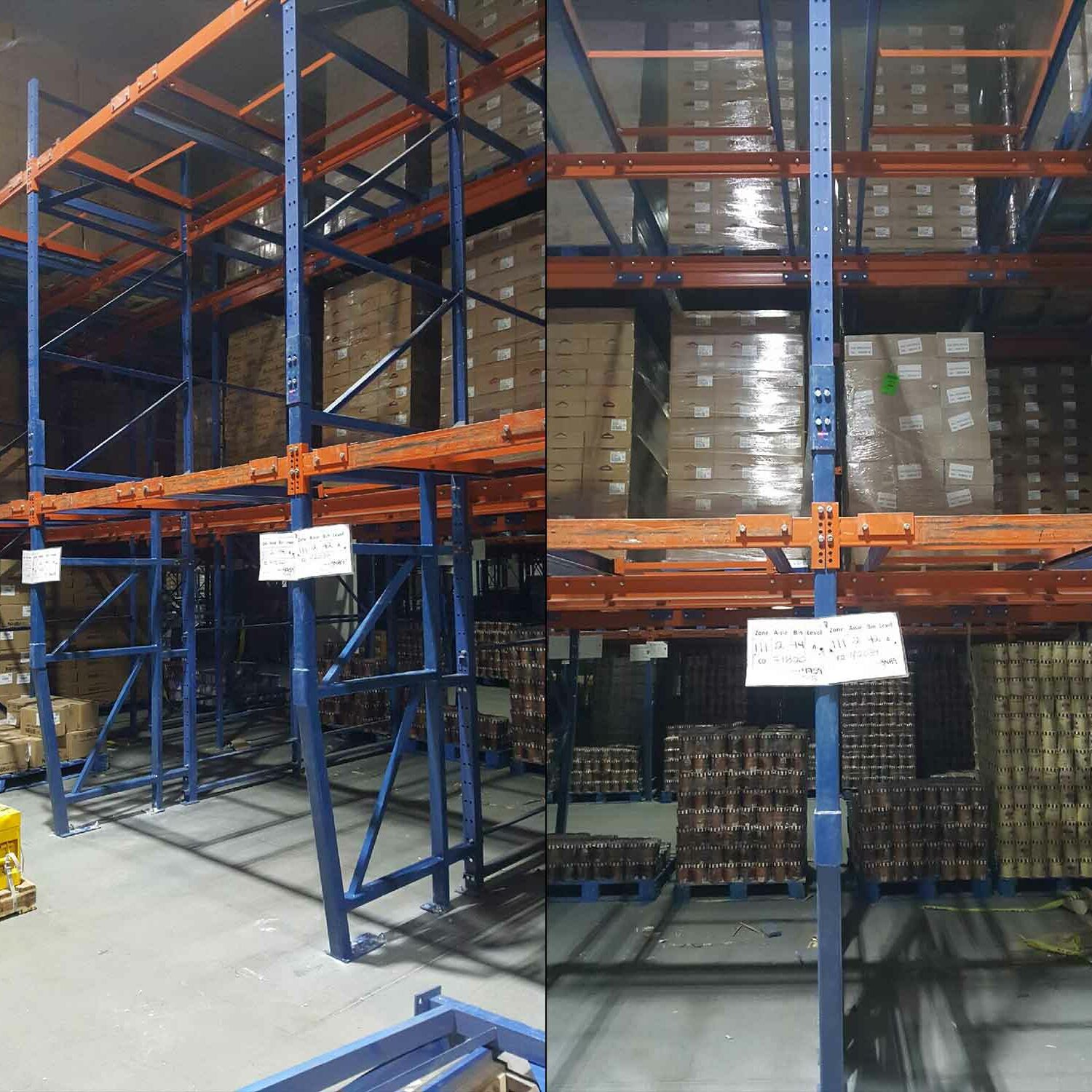
Freezer Fix – A Rack Repair Case Study
A food and beverage company wanted to address damaged selective rack in their freezer where they store pallets of frozen food.
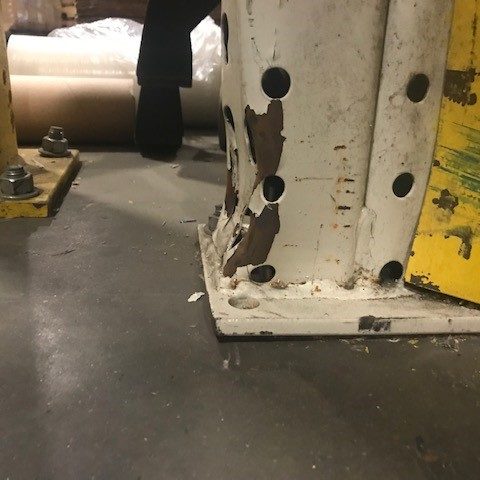
Routine Safety Inspection and Remediation Case Study
A company that stores boxes of records wanted to address rack safety concerns across their nationwide network of several hundred warehouses. They wanted to standardize their safety requirements.
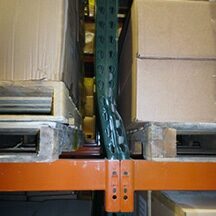
Retail Rack Rehab – A Case Study
A manufacturer of handbags wanted to address unsafe rack concerns in their 217,320 sq. ft. distribution center.
Related Warehouse Racking & Shelving Services
Discover the difference with us as your ultimate destination for comprehensive solutions. Experience the ease of entrusting us with every facet of your racking and shelving venture. Explore the range of services we offer: