Unit Load AS/RS Systems
A unit load AS/RS system, or automated storage and retrieval system, is an automated pallet storage solution that stores, tracks, picks and delivers pallets without human interaction other than dropping the pallet off and picking the pallet up. Unit load AS/RS generally falls into two categories: crane-based AS/RS systems and shuttle-based AS/RS systems.
Similar to pallet racking, there are different configuration types to consider when implementing a unit load AS/RS system. Choosing a storage configuration is a function of SKUs, throughput, area width and other factors. A system can range from:
-
- Single deep (1 pallet per lane)
- Double deep (2 pallets per lane)
- Triple deep (3 pallets per lane)
- Multi-deep or deep lane (4+ pallets deep)
If you’re looking for an AS/RS system for case or tote storage and retrieval, visit our mini load system page.
For companies that handle both pallets and cartons, a combination of a unit load AS/RS system and a mini load AS/RS system is a viable option.
How Unit Load AS/RS Systems Work
In most cases, pallets are transported to and from the system by a forklift. The forklift either drops the pallet off at the required aisle (meaning multiple possible drop off points) or at an automated induction system (meaning one drop off point for all pallets), which then takes the pallet to the correct aisle.
Here are the steps taken in both types of systems:
Crane-Based AS/RS System
- The systems scans the pallet to verify it’s the correct weight, size, and not leaning or falling apart.
- Either a forklift truck or an automated induction system brings the pallet to the correct aisle.
- It then places the pallet on a conveyor located on the ground level. Afterwards, the crane retrieves the pallet from the conveyor, transports it to the correct level of the system, and places it into the correct pallet position.
- Unloading works the same way: the crane retrieves the pallet from the system and transports it to the ground level conveyor at the receiving location. Pick the pallet up with either a forklift or an automated induction system and transported to the needed location.
Submit Your Inquiry
Shuttle-Based AS/RS System
- The system scans the pallet to verify it’s the correct weight, size, and not leaning or falling apart.
- A forklift truck or an automated induction system brings the pallet to the correct aisle.
- It then places the pallet on a lifter. There are two lifters per aisle that move vertically to get pallets from level to level.
- The pallet is then placed on to the lane shuttle. If the lane shuttle is occupied, the pallet is then placed on a buffer shuttle, which holds the pallet until the lane shuttle becomes available. This allows the lifter to remain active.
- The lane shuttle transports the pallet and places it in the correct pallet location.
- Unloading works the same way: the lane shuttle retrieves and transports the pallet to the lifter. The lifter transports the pallet to the ground level where it’s received by either a forklift or an automated induction system.
REB’s Turnkey Services for Unit Load AS/RS Systems
REB provides full project management of your unit load AS/RS system. A REB project manager will be your point of contact throughout the project. Our project managers prioritize communication and will make sure that all applicable parties have a firm understanding of timelines and progression of the project.
Read below to better understand our unit load AS/RS system project management services.
Design Services
The first step in REB's design services is to speak with your REB account executive so that we thoroughly understand the scope of your project. If necessary, we’ll conduct an onsite assessment. We want to make sure we understand your goals and current pain points so that we provide you with a solution that is optimized to your operation.
During the design process, we’ll obtain information such as your SKU profiles, space restrictions, and picking processes. We’ll work with you to ensure that your unit load AS/RS system is set up to suit your requirements. For example, if you require your system to have a first-in, first-out or a last-in, first-out product flow.
Once all information is obtained, REB project designers will create a CADD drawing of your unit load AS/RS system that suits all space and picking process requirements.
Permitting Support
If necessary, we’ll evaluate if permitting for your unit load AS/RS system is required through our permitting support services. If permits are required, we’ll put together and submit all drawings and other documentation needed for permit approval. This often includes a high pile storage report.
Subcontractor Management
Once your unit load AS/RS system design is finalized, your REB project manager will secure all suppliers and subcontractors. We’ll manage their involvement through the project. This includes freight and installation.
Our project management services prioritize communication and will make sure that all applicable parties have a firm understanding of timelines and progression of the project.
System Installation
REB Storage Systems has more than 60 years of professional experience installing material handling systems in warehouses nationwide. We’ll ensure that your operation’s unit load AS/RS system is safely installed and compliant with MHI & OSHA standards while it optimizes your storage space and improves efficiency.
Crane-Based vs. Shuttle-Based System
There are a number of factors that go into deciding which type of unit load AS/RS system is right for you. Three major things to take into account are:
- number of SKUs;
- number of pallets per SKU; and
- throughput requirement.
In general, if you have a low number of SKU’s paired with a high number of pallets per SKU, a shuttle-based system is ideal.
Conversely, if you have a high number of SKUs paired with a low number of pallets per SKU, a crane-based system is ideal.
These general guidelines can be overridden, though, depending on throughput requirements. For example, if you have a high number of SKUs paired with a low number of pallets per SKU, but require high throughput, a shuttle-based system may actually be more ideal for you. This is due to throughput limitations for crane-based systems.
For a more specific example of the above scenario: let’s say one crane can do 30 pallets per hour. If you require a 300 pallets per hour throughput, then you’ll need 10 cranes. With each crane requiring a 6 ft. aisle, this equates to a lot of space used to accommodate for the high number of cranes.
This is where a shuttle-based system starts to make more sense. You can use a 10-level shuttle system, each level handling 30 pallets per hour. This will allow for high throughput while more effectively utilizing your available storage space.
So as you can see, it’s a balancing act between a number of factors. A professional material handling company, such as REB, can evaluate your operation to help determine which is right for you.
Is a Unit-Load AS/RS System Right For Your Operation?
An AS/RS system is ideal for a large array of operational features. Some of these include:
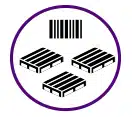
Low number of SKUs, high number of pallets per SKU (shuttle-based): Generally, if you have a high number of pallets of each SKU you will want deeper lanes so that each lane can house the large number of pallets of each SKU. Shuttles are able to retrieve pallets placed deep in the system.
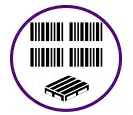
High number of SKUs, low number of pallets per SKU (crane-based): A crane-based system can accommodate up to 3 pallets deep. Since each lane should be designated to one SKU, generally a low number of pallets of each SKU makes more sense with a crane-based system.
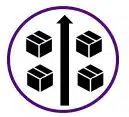
Availability to store higher than 30 ft.: Since a standard forklift’s reach is about 30 ft., this often limits the height of a traditional pallet rack system, resulting in wasted storage space. An AS/RS system will be able to utilize the entire available height of your DC.
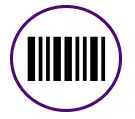
Stores products that require date code management or scan verification: This is often found with pharmaceuticals, medical supplies, and food distributors.
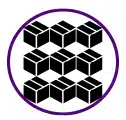
Stores heavy loads (crane-based): Crane-based AS/RS systems are able to handle very heavy loads, up to 6,000 lbs. This can be an ideal solution vs. having a forklift or other types of equipment placing and retrieving heavy loads within the system.
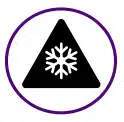
Freezer storage: AS/RS systems allow for the entire area of a freezer to be utilized, which is expensive real estate.
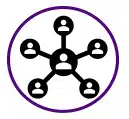
Have multiple DCs that could benefit from being consolidated into one: If you’re considering consolidating your DCs into one, an AS/RS system may be right for you. Consolidating DCs will cut down on costs overtime, since you’re not paying for extra real estate, employees, etc. Sounds like a no-brainer, right? But, there are challenges that many DCs face when considering this.
First, many companies don’t feel they can consolidate since it will mean higher throughput requirements for the one DC vs. multiple. An AS/RS system will allow for the higher throughput needed.
Secondly, consolidating means needing to house a large number of products in one building. The high density of an AS/RS system allows for this.
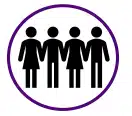
Lack of availability of consistent warehouse labor: One benefit of implementing an AS/RS system is it can cut down on labor costs. Less manpower is needed, since the system does much of the work. If you find yourself consistently taking time to hire and train new warehouse staff, an AS/RS system may be an ideal alternative.
Advantages of a AS/RS System
Labor reduction: less manpower is needed in an AS/RS system. Employees are no longer needed to travel great distances to store and load pallets. Pallets can be shipped just in time resulting in faster turnaround times. Additionally, systems can be placed right in front of dock doors for quick unloading and loading of trucks. These systems can also replenish picking areas.
Increased pick accuracy: systems can reach 99.95% pick accuracy or greater.
Utilizing full building height: since a standard forklift’s reach is about 30 ft., this often limits the height of a traditional pallet rack system. This results in wasted storage space. An AS/RS system will be able to utilize the entire available height of your DC.
Increased storage density (shuttle-based): in addition to being able to add vertical storage, a shuttle-based AS/RS increases storage density by storing deeper lanes than a pallet rack system.
For example, the pallet rack system that can store the deepest is a drive-in system. A drive-in system can technically go as deep as needed, however there are factors that limit how deep you’ll want to go. One example is the deeper you go, the higher the possibility of more damage via forklift in deeper lanes. Additionally, the deeper you go in drive-in rack, the more difficult it becomes to retrieve the pallets. So operational efficiency can become compromised.
A shuttle-based AS/RS system is basically unlimited as to how many pallets deep it can go, and the issues mentioned in regards to deep lane storage in drive-in rack are basically nonissues.
Ability to handle higher storage and throughput counts: if you want to achieve higher throughput, an AS/RS system is ideal. This ability to handle higher storage and throughput counts is another reason that this type of system allows companies to consolidate products in multiple DCs into one.
Reduces damage to products and the system: an AS/RS system eliminates product-to-product contact, which reduces the likelihood of product damage. Additionally, since a forklift operator does not have to retrieve pallets from within the system, damage to the storage structure is eliminated.
Your Next Step for an AS/RS System
Whether your next step is to gather more information or request a quote, consider REB Storage Systems. REB is a highly experienced systems integrator, in business since 1962. REB has 17 in-house project managers and project designers, all highly experienced in the material handling industry. These people know this industry inside and out.
REB is highly knowledgeable and experienced in designing and installing automation and racking solutions. We will make sure your system is the best fit for your SKU profiles and space. We work with you to provide a turnkey system. From design, products procurement, subcontractor management, install, and permitting support, REB handles it all for you.
We’d appreciate the opportunity to help you further, whether that be more information or a quote. Fill in the contact form on this page or call us at (800) 252-5955 to get in touch with a REB representative.