VLM + Selective + Push Back + Pallet Flow for Playground Equipment Storage – A Case Study
Solution at a Glance:
- Products Provided: Pick Module, Vertical Lift Module, Selective Racking, Push Back Racking, Pallet Flow Racking, Pallet Rack Protection
- Services Provided: System Design, Project Management, System Installation
- Location: Fon du Lac, WI
Concern: Inefficiency Due to Disjointed Operation
A playground equipment supplier was operating out of three buildings: their main warehouse, which was used for shipping and receiving orders, their out-building, which was used to store all their overflow inventory, and their office building. Having to transport their inventory between the two warehouses was inconvenient and time consuming.
The company decided it was best for them to consolidate their operations from three buildings into one. This building would have to store all the inventory that they kept between their two warehouses and accommodate for their continued growth.
Once they contracted with a new warehouse, the company hired REB to assess the facility so they could achieve all their goals. Because they had a wide variety of inventory that varies greatly in shape and size, REB would need to outfit the company’s new 126,000 square foot warehouse with several material handling systems that allows them to safely and efficiently store and pick their varied inventory, while also accommodating for their projected growth.
Solution: Consolidated Operation with a Pick Module
First, REB designers gained a thorough understanding of the company’s SKU characteristics, picking processes, building layout, and goals. They used this information to create a pick module layout optimized for these requirements. The pick module is comprised of four material handling solutions: selective racking, pallet flow racking, gravity flow racking, and vertical lift modules. In addition, safety products, such as row end protectors, were incorporated. Each of these solutions were carefully considered and chosen to promote the efficiency of the pick module as a whole.
Continue reading below to learn more about the systems that REB designed and built for the customer.
Vertical Lift Modules
The company was previously using a combination of selective racking and steel shelving to store their small pieces of inventory, such as brackets, bolts, and playground accessories. Subsequently, they used a rolling ladder cart when placing and picking items. This system took a considerable amount of time to pick products.
To increase storage density, picking accuracy, and throughput of these small parts, REB included a vertical lift module (VLM).
Density of these items is a high priority for the company, and the VLM stores these products in 75% less space than traditional racking or shelving. More specifically, for the company to store their small parts on shelving it would require 1,600 sqft of shelving space. With the VLMs, the same products are stored in an area of only 395 sqft.
Increased picking accuracy and decreased pick times were also of high priority. The VLM achieves this by allowing the picker to remain in one location while the required products come to them. When items are needed, the picker simply inputs these items into the VLM’s touchscreen interface. The VLM then automatically retrieves each item, which is stored on one of several trays located within the unit and brings it to the front for the picker. Once the tray is out and ready to be picked from, the VLM will shine a laser to the compartment in which the required product is stored. The picker then indicates on the touch screen that they have picked the item, at which time the VLM simultaneously puts away that tray away and brings forward the next required tray.
Because the company has several small parts that are often bundled together, known as kitting, decreased pick times are also seen through strategic placement of these items on the same tray within the VLM.
Selective Racking
Because much of their playground equipment is bulky and oddly shaped, it cannot be palletized. The versatility of selective racking makes it best suited for this type of inventory. REB designed a selective racking system of 680 bays made up of 7 different bay sizes tailored to their product range. The bay sizes range from 30” deep, for small parts storage, to 168” deep, for large playground items.
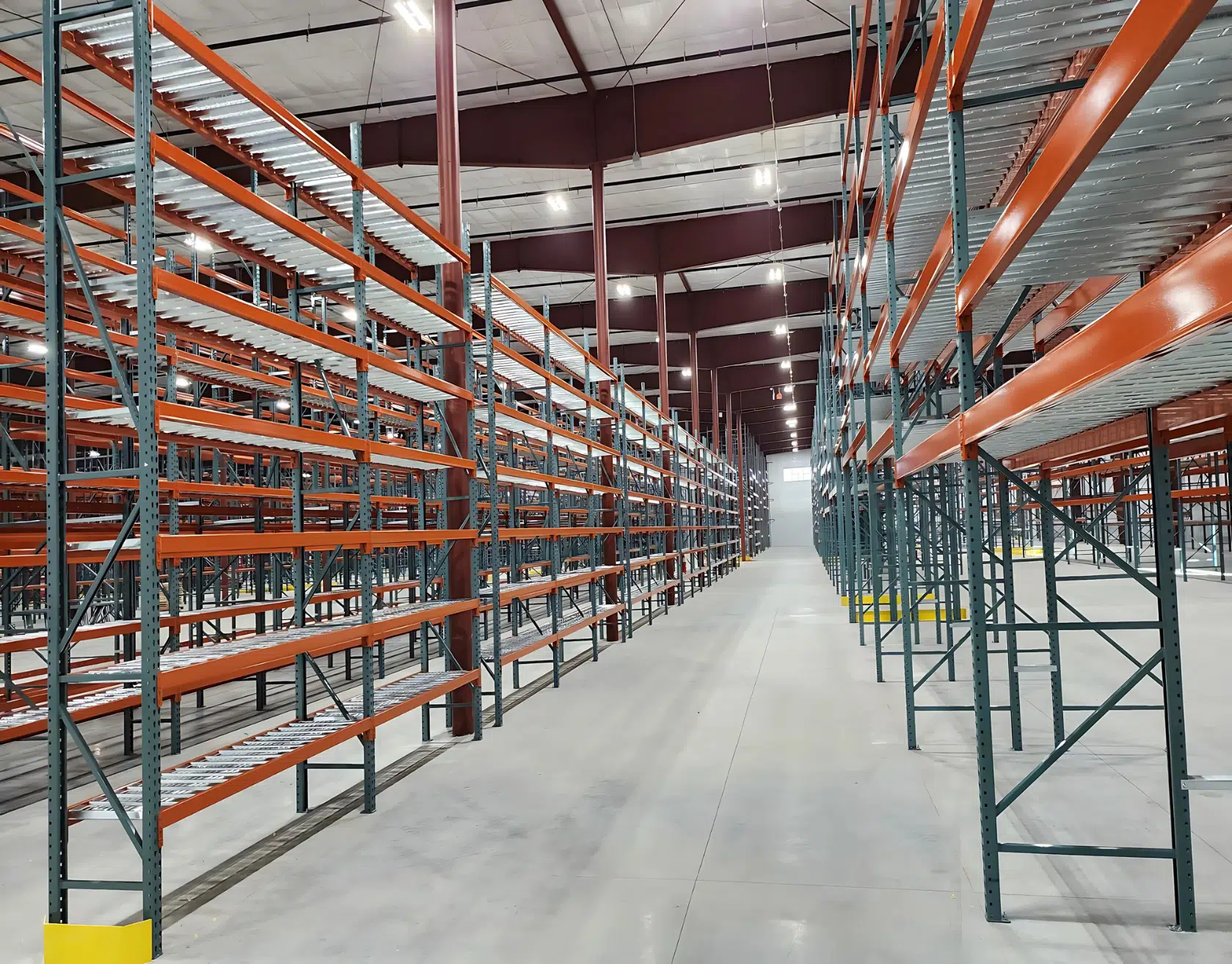
Some of their inventory is too large to fit on the selective racking. These items are stored on carts so that they are easily accessed and transported. Their previous layout required the carts to be kept within the aisles of the warehouse. Consequently, they were often in the way of pickers and had to be moved around, causing major inefficiencies. To keep the aisles clear, REB’s design includes a section of 6-deep selective rack with an egress aisle, which provides a designated area for the carts to be parked in.
Push Back Racking
Certain pieces of inventory that the company stores are kept in gaylords, which are containers attached to pallets. This portion of the company’s inventory was previously stored on the floor of the warehouse, since their racking system was modified for small parts storage. This approach to storing their palletized inventory had glaring flaws that resulted in safety and efficiency issues.
REB designed a push back rack system for this palletized inventory. This 6-deep system provides more than 800 pallet positions and is ideal for the storage of palletized, non-date-sensitive inventory. It allows the customer to store higher counts of the same SKU in a highly efficient and high-density manner.
Push back systems are gravity flow systems, meaning once the front pallet is picked, the next one automatically flows to the front pick position. This, combined with being able to store the same SKU within the same rows, greatly improves the pick time of the company’s products. It keeps their SKUs neatly organized to improve overall warehouse efficiency.
Pallet Flow Racking
Because some of the company’s inventory benefits from first-in, first-out (FIFO) inventory rotation, REB integrated pallet flow racking within the pick module. Pallet flow rack provides similar benefits as push back rack, such as high density and gravity flow, but with FIFO inventory management. However, pallet flow does require an additional aisle to accomplish this, making it slightly less dense in the overall layout than push back rack.
REB designed a 6-deep pallet flow system with more than 700 pallet positions. This improves the company’s operation by providing higher density, higher selectivity, and increased efficiency. Because this system provides FIFO inventory management, they can easily rotate inventory.
Pallet Rack Protection
To help keep all the above pallet racking safe from damage, REB installed row end protection to each row of racking. The investment in such protection could ultimately save the company from having to replace the systems and help keep their employees and inventory safe.
Outcome: Efficient Operations Under One Roof
The successful implementation of all the above systems into one pick module has allowed the company to reduce their operations to a single location. Despite consolidating the operations of 3 separate buildings into one single building, the company now stores more inventory and operates more efficiently than ever before.
Optimize Your Facility with REB Storage
If you feel like you’re using an out-of-date inefficient system, contact REB today.
Our dedicated team of material handling experts will work with you to provide you with a solution that will optimize your picking operations. We are highly experienced in identifying inefficiencies and implementing improved systems. Our project design and project management teams bring more than 500 years of combined experience to every project.
We’d appreciate the opportunity to help you further, whether that be more information or a quote. Fill out the contact form on this page or call us at (800) 252-5955 to get in touch with a REB representative.
Share this post:
Submit Your Inquiry
Since 1962
REB has completed more than 100,000 projects in 15 countries (including all 50 states) for more than 20,000 customers across 50 industries, with 70% of customers as repeat buyers.
This is made possible by our team that has more than 300 years of industry experience designing and project managing material handling systems.
Learn more about REB's award winning service.