3 Warehouse Layout Patterns & Product Flow Examples
Your warehouse product flow determines your overall productivity and efficiency. Watch this video to learn about three layout options to consider (1-minute, 36-seconds).
VIDEO TRANSCRIPT
Hi and welcome to this edition of Total Warehouse Tutorials. In this video we will discuss various warehouse layouts and product flow options.
Your warehouse product flow determines your overall productivity and efficiency. When creating a warehouse rack design overall layout of your warehouse the shipping and receiving placement should be evaluated and chosen based on your available space, product throughput needs, and available resources.
Warehouse layout options to consider include U-shaped, I-shaped and L-shaped patterns.
A U-shaped warehouse product flow is the most common type of layout. In this layout the shipping and receiving docks are located next to one another, offering shared utilization of dock resources such as personnel and material handling equipment. This layout also minimizes product handling, offering high cross-docking capability.
I-shaped warehouse product flow and L-shaped warehouse product flow, also known as through flow, are similar in that the shipping and receiving areas are located on different sides of the warehouse. As a result, these require more available warehouse space than U-shaped layouts.
These layouts can be beneficial for certain operations. For example, warehouses that require heightened security can benefit from the separate “in” and “out” areas. I-shaped and L-shaped layouts can also provide larger sorting and storage areas for both shipping and receiving docks as well as allowing for isolated monitoring of each function.
That’s it for this edition of Total Warehouse Tutorials. I hope you join us for our next one in which we will discuss various conveyor system types.
Common Warehouse Layout Product Flow Options
Your warehouse product flow determines your overall productivity and efficiency. Warehouse and distribution center layouts often include four areas: dynamic storage, static storage, shipping, and receiving. How these areas are configured should be based your available space, product throughput needs, and material handling systems used.
This page examines the difference between dynamic and static storage, warehouse layout options, and FIFO vs. LIFO storage. Implementing these to fit your operation’s needs will result in an efficient warehouse.
Dynamic Storage & Static Storage
Incorporating dynamic and static storage areas can help improve throughput. Your warehouse layout and nature of your product flow will determine where your dynamic and static storage areas should be within the warehouse. Both dynamic and static storage hold different benefits to warehouse efficiency. Read below to find out how each should be utilized.
Dynamic Storage
Dynamic storage, also known as forward pick, is the section of warehouse in which items are consistently picked for order fulfillment. In this area, high selectivity is vital to a successful operation. Therefore, dynamic storage often integrates multiple types of racking to reduce overall pick time, also known as a pick module.
Dynamic Storage Functions
- Offers high selectivity.
- Allows for the combination of multiple rack types to create a pick module.
- Reduces overall picking time.
Dynamic Storage and Pick Modules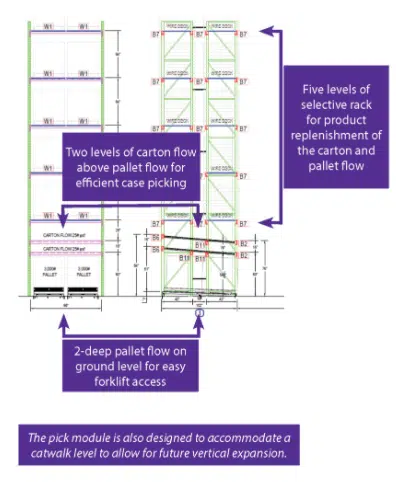
A pick module can consist of one or multiple pick levels and can be designed in a number of configurations tailored to the material handling equipment used and product characteristics. For example, as shown in the illustration to the right, pallet flow, carton flow, and selective rack are integrated together to expedite the order fulfillment process. This example shows 2-deep pallet flow on the ground level, which provides first-in, first-out pallet storage that can be easily accessed by forklifts. Carton flow rack is integrated above the pallet flow for first-in, first-out case or piece picking. Selective rack is included above these picking locations to be used for product replenishment in the carton flow and pallet flow areas.
Static Storage
The static storage area of a warehouse is where the overflow of product is stored, typically on pallets. This section of the warehouse is also referred to as the reserve storage area. Once products in the dynamic storage area are picked, pallets are retrieved from static storage for replenishment.
Static Storage Functions
- Reserve pallet storage.
- Offers high density storage.
Warehouse Product Flow Layouts
There are a number of warehouse layout options to choose from when designing your warehouse layout. The size of your warehouse and the nature of your product will determine which warehouse layout to choose. Read about three of the most common warehouse layout types below.
U-Shaped Warehouse Product Flow
A U-Shaped warehouse layout is the most common layout. In this layout the shipping and receiving docks are located next to one another, offering shared utilization of dock resources such as personnel and material handling products. This layout also minimizes product handling, offering high cross-docking capabilities.
L-Shaped & I-Shaped Warehouse Product Flow
L-Shaped warehouse product flow and I-Shaped warehouse product flow, also known as through flow, are similar in that the shipping and receiving areas are located on different walls of the warehouse.
These layouts can be beneficial for certain operations. For example, warehouses that require heightened security can benefit from the separate “in” and “out” areas. I-shaped and L-shaped layouts can also provide larger sorting and storage areas for both shipping and receiving docks as well as allowing for isolated monitoring of each function.
L-Shaped Layout
L-Shaped warehouse layouts are designed for shipping and receiving areas to be located on adjacent walls of the warehouse. This design allows for products to be stored in-between the designated shipping and receiving docks, expanding storage to the back of the warehouse.
I-Shaped Layout
I-Shaped Warehouse layout allows for product flow to move from one end to the other, in a straight line. In an I-shaped layout, storage is located directly in the middle of each loading and unloading dock. I-Shaped warehouses are ideal for operations that require high-volume storage.
Storage Systems Product Flows: First-In-First-Out vs. Last-In-First-Out
How your warehouse racking layout will look is dependent on your warehouse product flow requirements. Racking systems can be categorized in two groups, first-in, first-out and last-in, first-out.
First-In, First-Out Storage Racking Types
First-in, first-out (FIFO) storage allows product placed into the system first, to be the first removed. You should consider FIFO storage when:
- Your operation has a high inventory turnover rate.
- You will be storing inventory with expiration dates.
- Your operation requires rapid stock rotation.
Drive-Through Rack
- The rack supports inclined rollers or wheels that allow cartons to glide from the back (loading) aisle to the front (picking) aisle.
- Incorporates gravity system that provides excellent volume utilization.
Ideal Uses
- Storage of frozen or chilled product.
- High volume case-pick and piece-pick.
- Can be combined with other rack types to create a pick module.
Key Features
- Highly customizable.
- Provides high density storage.
- Highly durable.
- Decreases pick times.
- Option to add breaks for speed control.
Carton Flow Racking
- Lift trucks are able to enter through both ends of the system for loading and unloading.
- Drive-through rack can be convenient, but require an additional aisle.
Ideal Uses
- A warehouse or distribution setting.
- Continuous product circulation.
- You require access to all palletized items simultaneously.
- Storage of retail product, food, and beverage – although can store many other items.
Key Features
- Eliminates the need for down-aisle picking aisles.
- Easily can be deconstructed and reconfigured as needed.
- High density allowing for increased warehouse space.
- Can be designed to suit specific pallet types.
Pallet Flow Rack
- Designed for larger inventory movement on pallets.
- Supports inclined rollers or wheels that allow cartons to glide from the back (loading) aisle to the front (picking) aisle.
Ideal Uses
- Storage of frozen or chilled product.
- Materials that vary in size.
- Best suits high quality pallets.
- Storage can range from 2-12+ pallets deep.
- Provides excellent volume utilization.
- Customizable
- Offers high selectivity and high density.
- Can be combined with other rack types to create a pick module.
- Breaks can be included.
Last-In, First-Out Storage Racking Types
Last-in, first-out (LIFO) storage allows the last product placed into the system to be removed first. LIFO storage is ideal when:
- Your product has long shelf life.
- Your product will or can be stored in bulk.
- Your product is not perishable.
Drive-In Rack
- Lift trucks load and unload by entering through the front of the system and then back out.
Ideal Uses
- Sorting large quantities of homogeneous product.
- Storing products with long life spans.
- Storing products that require large, one time moves.
Key Features
- Eliminates the need for down-aisle picking aisles.
- Drive-in rack offers higher density than drive through rack.
- Lower selectivity, higher density.
- Can support cooler or freezer storage.
Selective Pallet Rack
- Pallets are loaded and unloaded from the front via lift truck.
- Enables direct access to all pallets or cartons without needing to move others.
Ideal Uses
- A warehouse or distribution center setting.
- Continuous product circulation.
- Require access to all palletized items simultaneously.
- Storage of retail product, food, and beverage – although can be used to store other products.
- May be used for reserve storage.
Key Features
- Most common racking type.
- Offers high selectivity with lower density.
- Most common bay size 96″ wide x 42″ deep.
Push Back Rack
- The rack supports carts that move along inclined rails.
- Utilizes the warehouse cube to reduce required aisle space and maximize product storage.
Ideal Uses
Key Features
- Variety of configurations available with bay widths that accommodate single-wide or double-wide pallet rows.
- High density storage.
- Rack can be as high as needed.
- Allows access to multiple groups of SKUs simultaneously.
- More efficient picks, each lane can hold a particular SKU.
Combining Multiple Rack Types Into A Pick Module
- Warehouse pick modules can include a number of elements in one design to produce the optimal layout and flow process for your operation.
- Pick module layouts vary, but often contain areas to accommodate faster moving and slower moving products and/or palletized products and piece picking.
- Manual pick applications.
- Automated pick applications.
- A combination of both manual and automated.
Key Features
- Customizable to your operation.
- Can be compromised of the multiple racking types listed above.
- Can be one level or multiple levels.
- Reduce or eliminate walking time.
- Saves labor costs.
- Shortened time for order fulfillment.
- Increased pick accuracy, selectivity, and density.
Your Next Steps For Your Warehouse Layout
Now that you have a better idea of what warehouse layouts are available, we’d appreciate the opportunity to help you with the next step. Whether you are certain which layout will work for you or you need more guidance, our experts are ready to assist you.
REB has a talented team of in-house project managers and project designers, all highly experienced in the material handling industry. We’ll work with you to make sure that your system is the best fit for your operation, installed and completed on-time and within budget.
We’d appreciate the opportunity to help you further, whether that be more information or a quote. Fill in the contact form on this page or call us at (800) 252-5955 to get in touch with a REB representative.
Share this post:
Submit Your Inquiry
Since 1962
REB has completed more than 100,000 projects in 15 countries (including all 50 states) for more than 20,000 customers across 50 industries, with 70% of customers as repeat buyers.
This is made possible by our team that has more than 300 years of industry experience designing and project managing material handling systems.
Learn more about REB's award winning service.